1 Pictures Show
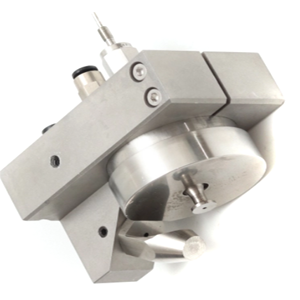
2 Technical Parameters
Model | Frequency | Power | Average partice | Maximum volume | Liquid viscosity < CPS | Atomizing head structure | Medium | Applicable |
GPN-15500 | 15 | 500 | 62 | 150L/h | 1500cp | Trumpet shaped | Ordinary water, various liquid substances, chemical liquids, various oils, viscous liquids, metal melts | Atomization and humidification, chemical mixing, production, spray drying granulation, paint spraying, metal powder making |
GPN-20300 | 20 | 300 | 51 | 70L/h | 1000cp | Trumpet shaped |
GPN-30100 | 30 | 100 | 39 | 50L/h | < 100 | Trumpet shaped |
GPN-4060 | 40 | 60 | 32 | 10L/h | < 100 | Focus /Conical/Flat (Optional ) |
GPN-5030 | 50 | 30 | 28 | 2L/h | < 100 |
GPN-5530 | 55 | 30 | 28 | 2L/h | < 100 |
GPN-6020 | 60 | 20 | 20 | 1L/h | < 100 |
GPN-8020 | 80 | 20 | 25 | 1L/h | < 100 |
GPN-10020 | 100 | 20 | 25 | 1L/h | < 100 |
GPN-12030 | 120 | 20 | 20 | 1/h | < 100 |
Customized to Customer Requirements |
|
|
|
3 Nozzle Type
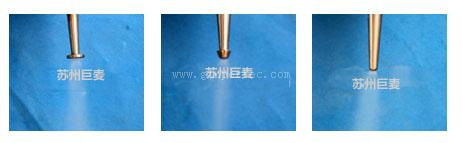
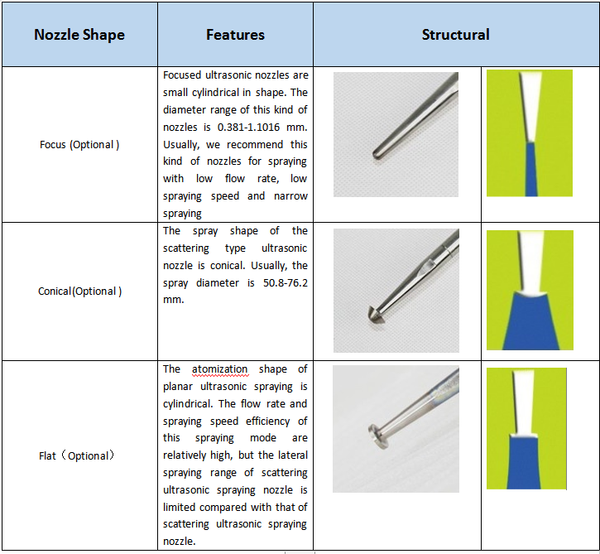
Ultrasonic spraying, also known as ultrasonic spraying, is a spraying process using ultrasonic atomization technology. The material to be sprayed is first in a liquid state, and the liquid may be a solution, a sol, a suspension, etc., and the liquid coating is first atomized into fine particles by an ultrasonic atomizing device, and then uniformly coated on the surface of the substrate by a certain amount of carrier gas. Thereby forming a coating or film. The biggest difference between ultrasonic spraying and traditional single-fluid or two-fluid spraying is that the atomizing device or the atomizing nozzle adopts an ultrasonic atomizing device, that is, an ultrasonic nozzle.
The main advantages of ultrasonic spraying are:
1. High uniformity of coating
The uniformity of liquid particle distribution after atomization by the ultrasonic nozzle is significantly higher than that of the two-fluid nozzle, which is also known as the air spray gun, so that the uniformity of the coating after the ultrasonic nozzle is sprayed is improved. In general, ultrasonic spray coating uniformity can reach more than 95%.
2. High raw material utilization rate and less spatter
Since ultrasonic spraying is liquid atomization by ultrasonic vibration, the process of atomization of the coating does not require any gas, that is, the atomization process does not require pressure, and only a low carrier gas pressure is applied after atomization to transport the liquid mist. The liquid rebound and splash caused by the two-fluid spray high-pressure air are greatly reduced, thereby greatly improving the utilization of the paint. The utilization rate of raw materials for ultrasonic spraying is more than 4 times that of ordinary air spraying, and the utilization rate can be up to 90% or more.
3. High precision of coating thickness control
The main factor affecting the thickness accuracy of the coating is the spray flow rate of the paint, that is, the amount of load on the substrate per unit time. The ultrasonic nozzle does not have any pressure on the liquid, so the flow rate of the sprayed coating liquid can be controlled completely by the high-precision metering pump, thereby realizing high-precision spray flow control. Such as high-precision syringe pump, its flow control accuracy can reach the level of picoliter per second, and the micro-channel design of the ultrasonic nozzle can also achieve nano-second control accuracy.
4. The coating thickness is thin and can reach several tens of nanometers.
Since the spray volume of the ultrasonic jet can achieve a very low steady flow rate (0.001 ml/min), it can achieve a very small amount of loading on the substrate, thereby achieving a very thin dry film. For some nanomaterials, the dry film thickness can be as low as tens of nanometers. It can be used to prepare glass films such as transparent conductive films, antireflection films, thermal barrier films, and hydrophobic and hydrophobic films.