1. Principle
Cutting technology
The main function of the ultrasonic cutting process is to split the connected parts. By vibrating at a high frequency per second, the pressure on the item to be cut can be reduced. This results in a neat and clean cutting surface. In practical application, it is divided into two processes, separation welding and cutting.
Separation welding
The thermoplastic multi-layer textile, non-woven material or film can be cut into any shape by ultrasonic wave and welded along the cutting profile at the same time. The thermoplastic fiber content should be at least 20%. The cutting anvil with the corresponding cutting profile is cut by vibration generated by the ultrasonic system. At the same time, vibration attenuation generates heat in the cutting zone, which leads to welding along the cutting edge.
Cutting
The ultrasonic vibrating blade separates the item to be cut quickly and precisely with minimal resistance and without residue. Ultrasound has been used in finished product cutting for many years. When cutting baked foods, energy bars, cheese, pizza and other materials, vibrating (cold) cutting heads reduce resistance during the cutting process and remove adhering product residue. The result: a flat surface that can be re-cut without deformation or thermal damage to the product.
2. Application
2.1. Synchronous extension cutting: cutting and sealing are performed and completed simultaneously. The two ends of the welded fiber can be cut simultaneously within a micron, which is a clear advantage in medical and filtration technologies requiring high quality
2.2. Continuous cutting and sealing: the advantage of ultrasonic cutting and sealing technology is that in continuous operation, textile fabrics and non-woven fabrics can be quickly and accurately sealed and cut.
2.3. Ultrasonic Cutting and welding: the flexible cutting of polymer and textile components must ensure the fastest speed and accuracy of cutting edges, and ultrasonic processing is an ideal process in the automotive industry.
2.4. Ultrasonic allocation: ultrasonics cut products accurately and quickly with minimal resistance through high-speed vibration, and achieve no residue, no deformation and no thermal damage on the product surface.
2.5. Ultrasonic Separated solid material: using ultrasonic frequency to drive cutter vibration can easily cut into the material, and very accurate and material saving.
2.6 Cutting solid material: Ultrasonic vibrations are transmitted via the welding head to the installed cutting edge to cleanly cut different materials, producing perfect sections such as carbon fiber or rubber products.
3. Technical Parameters
Frequency | Power range | Input Voltage | Control Way |
20-40KHZ |
100-2000W |
220V | PLC+ touch screen, manual and automatic modes, with handle control |
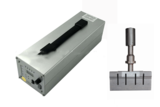
